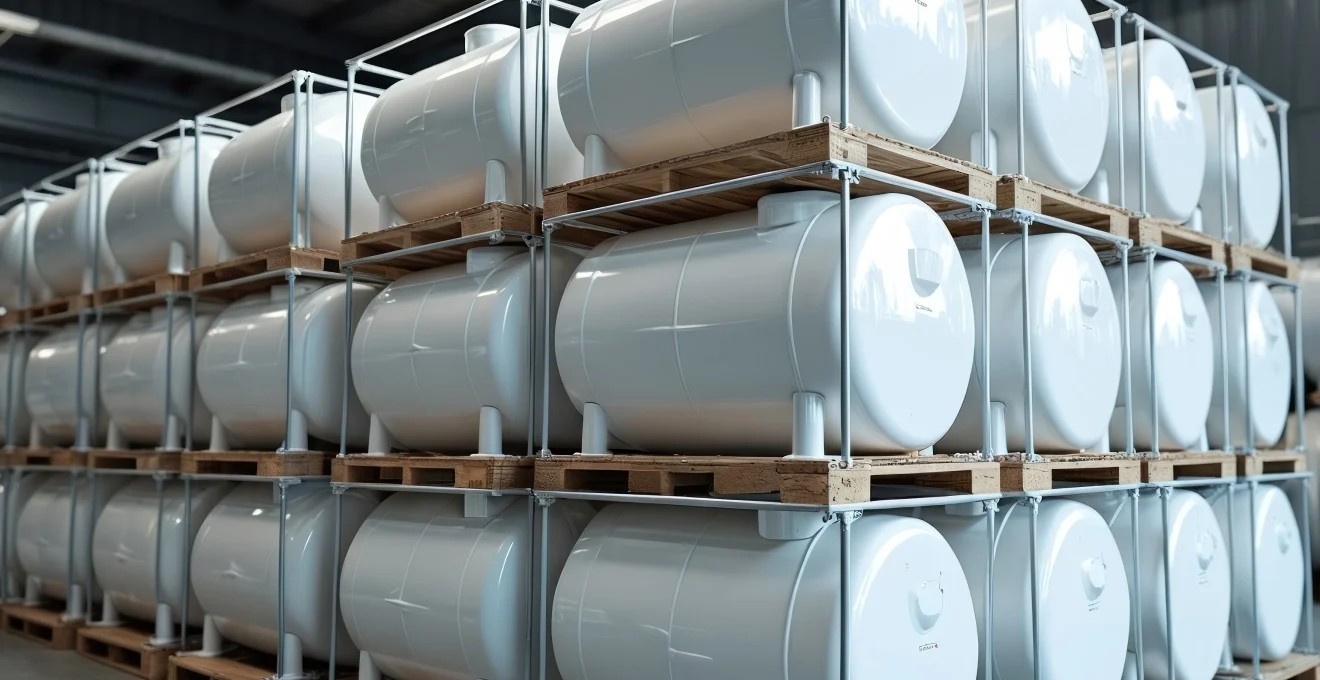
Le stockage de carburant est un enjeu crucial pour de nombreuses industries et particuliers. Choisir la bonne cuve de stockage peut faire toute la différence en termes de sécurité, de durabilité et d'efficacité opérationnelle. Que vous soyez un professionnel du secteur pétrolier, un gestionnaire de flotte ou un particulier cherchant à stocker du carburant pour votre propre usage, comprendre les différentes options disponibles est essentiel. Ce guide détaillé vous aidera à naviguer parmi les différents types de cuves, leurs caractéristiques spécifiques et les réglementations à respecter pour un stockage optimal et sécurisé de vos carburants. Pour en savoir plus sur les meilleures pratiques de stockage de carburant et les solutions adaptées à vos besoins spécifiques, n'hésitez pas à consulter les experts de stockagecarburant.com. Leur expertise vous guidera dans le choix et la gestion optimale de vos installations de stockage de carburant.
Types de cuves de stockage de carburant : caractéristiques et applications
Le choix d'une cuve de stockage de carburant dépend de plusieurs facteurs, notamment le type de carburant à stocker, le volume nécessaire, l'emplacement et les conditions environnementales. Les principaux types de cuves se divisent en deux catégories : les cuves métalliques et les cuves en plastique. Chacune présente des avantages et des inconvénients spécifiques qui doivent être pris en compte lors de la sélection.
Les cuves métalliques sont réputées pour leur robustesse et leur longévité, tandis que les cuves en plastique offrent une plus grande légèreté et une résistance accrue à la corrosion. Le choix entre ces deux options dépendra souvent de l'application spécifique et des contraintes du site de stockage. Par exemple, une station-service aura des besoins différents d'une exploitation agricole ou d'un site industriel.
Il est également important de considérer les réglementations en vigueur, qui peuvent varier selon la capacité de stockage et le type de carburant. Ces normes visent à garantir la sécurité et la protection de l'environnement, deux aspects essentiels dans le domaine du stockage de carburant.
Cuves métalliques : résistance et durabilité pour le stockage de carburant
Les cuves métalliques sont largement utilisées dans l'industrie du stockage de carburant en raison de leur robustesse et de leur capacité à résister à des conditions environnementales difficiles. Elles sont particulièrement adaptées pour le stockage à long terme de grands volumes de carburant. La durabilité des cuves métalliques en fait un choix privilégié pour les installations permanentes et les sites à forte activité.
L'un des principaux avantages des cuves métalliques est leur résistance aux chocs et aux pressions élevées. Cette caractéristique est particulièrement importante dans les environnements industriels où les risques de dommages mécaniques sont plus élevés. De plus, les cuves métalliques peuvent être facilement modifiées ou réparées sur site, ce qui prolonge leur durée de vie et réduit les coûts de remplacement à long terme.
Cependant, le poids élevé des cuves métalliques peut compliquer leur transport et leur installation, en particulier dans des zones d'accès difficile. De plus, sans traitement approprié, elles peuvent être sujettes à la corrosion, un facteur à prendre en compte lors de la planification de la maintenance à long terme.
Cuves en acier inoxydable : prévention de la corrosion et longévité
Les cuves en acier inoxydable représentent une solution de premier choix pour le stockage de carburant, en particulier dans des environnements corrosifs. Leur résistance naturelle à la corrosion les rend idéales pour le stockage à long terme de divers types de carburants, y compris ceux contenant des additifs agressifs. Cette caractéristique permet de réduire considérablement les coûts de maintenance et de prolonger la durée de vie de l'installation.
L'acier inoxydable offre également une excellente résistance aux variations de température, ce qui est crucial pour maintenir la qualité du carburant stocké. De plus, sa surface lisse facilite le nettoyage et réduit le risque d'accumulation de résidus, un aspect important pour maintenir la pureté du carburant.
Bien que l'investissement initial pour une cuve en acier inoxydable soit plus élevé, le retour sur investissement à long terme est souvent avantageux grâce à sa durabilité et ses faibles besoins en maintenance. Pour les installations qui nécessitent une fiabilité maximale et une longue durée de vie, l'acier inoxydable est souvent le matériau de choix.
Réservoirs en aluminium : légèreté et mobilité pour applications spécifiques
Les réservoirs en aluminium offrent une alternative intéressante pour certaines applications spécifiques de stockage de carburant. Leur principal avantage réside dans leur légèreté, qui facilite grandement le transport et l'installation, en particulier dans des zones d'accès difficile ou pour des applications mobiles. Cette caractéristique en fait un choix privilégié pour les équipements de ravitaillement mobile ou les installations temporaires.
L'aluminium présente également une bonne résistance à la corrosion, ce qui réduit les besoins en maintenance par rapport à certains aciers non traités. De plus, sa conductivité thermique élevée peut être avantageuse pour maintenir la température du carburant stable dans certaines conditions climatiques.
Cependant, il est important de noter que les réservoirs en aluminium sont généralement moins résistants aux chocs et aux pressions élevées que leurs homologues en acier. Ils sont donc plus adaptés pour des applications à plus petite échelle ou des environnements moins exigeants. Le choix d'un réservoir en aluminium doit être soigneusement évalué en fonction des conditions spécifiques d'utilisation et des réglementations en vigueur.
Revêtements époxy : protection renforcée des cuves métalliques
Les revêtements époxy jouent un rôle crucial dans la protection des cuves métalliques contre la corrosion et l'usure. Ces revêtements créent une barrière imperméable entre le métal et le carburant stocké, prolongeant ainsi considérablement la durée de vie de la cuve. L'application d'un revêtement époxy est particulièrement recommandée pour les cuves en acier standard, qui sont plus susceptibles de se corroder au fil du temps.
Le processus d'application d'un revêtement époxy nécessite une préparation minutieuse de la surface de la cuve pour assurer une adhérence optimale. Une fois appliqué, le revêtement offre non seulement une protection contre la corrosion, mais améliore également la résistance chimique de la cuve, la rendant plus apte à stocker une variété de carburants et d'additifs.
Il est important de noter que même avec un revêtement époxy, des inspections régulières sont nécessaires pour détecter tout signe d'usure ou de dégradation du revêtement. Un entretien adéquat et des réparations ponctuelles peuvent considérablement prolonger l'efficacité du revêtement et, par conséquent, la durée de vie de la cuve.
Normes EN 12285 et NF M 88-940 : conformité des cuves métalliques
La conformité aux normes est un aspect crucial dans le choix et l'installation des cuves métalliques pour le stockage de carburant. Les normes EN 12285 et NF M 88-940 sont particulièrement importantes dans ce domaine, établissant des critères stricts pour la conception, la fabrication et les tests des cuves métalliques.
La norme EN 12285 se divise en deux parties : la partie 1 concerne les cuves horizontales cylindriques à simple et double paroi pour le stockage enterré de liquides inflammables et non inflammables polluant l'eau, tandis que la partie 2 traite des cuves horizontales cylindriques à simple et double paroi pour le stockage aérien de liquides inflammables et non inflammables polluant l'eau.
La norme NF M 88-940, quant à elle, spécifie les exigences pour les réservoirs en acier de capacité inférieure ou égale à 10 m³, destinés au stockage non enterré de produits pétroliers liquides. Cette norme est particulièrement pertinente pour les installations de plus petite taille ou les applications domestiques.
Le respect de ces normes garantit non seulement la sécurité et la fiabilité des cuves, mais aussi leur conformité aux exigences réglementaires. Il est donc essentiel de vérifier que les cuves choisies sont certifiées conformes à ces normes avant toute installation.
Cuves en plastique : polyéthylène et alternatives synthétiques
Les cuves en plastique, notamment celles en polyéthylène haute densité (PEHD), gagnent en popularité dans le domaine du stockage de carburant. Leur légèreté, leur résistance à la corrosion et leur facilité d'installation en font une option attrayante pour de nombreuses applications. Ces cuves sont particulièrement adaptées aux installations où le poids est un facteur limitant ou dans des environnements où la corrosion est une préoccupation majeure.
L'un des principaux avantages des cuves en plastique est leur résistance aux agents chimiques présents dans les carburants modernes. Cette caractéristique les rend particulièrement adaptées au stockage de biocarburants ou de carburants contenant des additifs agressifs. De plus, leur surface intérieure lisse réduit l'accumulation de résidus et facilite le nettoyage.
Cependant, il est important de noter que les cuves en plastique peuvent être plus sensibles aux dommages mécaniques et aux variations de température extrêmes que leurs homologues métalliques. Le choix d'une cuve en plastique doit donc être soigneusement évalué en fonction des conditions spécifiques du site de stockage et des exigences réglementaires locales.
Cuves en PEHD : résistance chimique et facilité d'installation
Les cuves en polyéthylène haute densité (PEHD) sont devenues une option de plus en plus populaire pour le stockage de carburant, en particulier dans les applications de moyenne capacité. Le PEHD offre une excellente résistance aux produits chimiques, ce qui le rend particulièrement adapté au stockage de divers types de carburants, y compris les biocarburants et les mélanges contenant des additifs agressifs.
L'un des principaux avantages des cuves en PEHD est leur légèreté, qui facilite considérablement le transport et l'installation. Cette caractéristique est particulièrement appréciée dans les zones d'accès difficile ou lorsque des modifications fréquentes de l'agencement sont nécessaires. De plus, le PEHD est naturellement résistant à la corrosion, ce qui élimine le besoin de traitements de surface ou de revêtements protecteurs coûteux.
Il est important de noter que bien que les cuves en PEHD soient résistantes aux produits chimiques, elles peuvent être plus sensibles aux dommages mécaniques et aux variations de température extrêmes que les cuves métalliques. Une attention particulière doit donc être portée à leur installation et à leur protection contre les impacts potentiels.
Réservoirs en PRFV : fibre de verre pour applications spécialisées
Les réservoirs en plastique renforcé de fibre de verre (PRFV) représentent une solution avancée pour le stockage de carburant dans certaines applications spécialisées. Le PRFV combine la légèreté et la résistance chimique du plastique avec la robustesse supplémentaire apportée par les fibres de verre, offrant ainsi un excellent compromis entre durabilité et facilité de manipulation.
Les cuves en PRFV sont particulièrement appréciées pour leur résistance exceptionnelle à la corrosion et leur capacité à supporter des pressions internes élevées. Cette caractéristique les rend idéales pour le stockage de carburants sous pression ou dans des environnements corrosifs. De plus, la flexibilité de conception du PRFV permet de créer des formes complexes adaptées à des espaces restreints ou des configurations spécifiques.
Cependant, il est important de noter que les cuves en PRFV peuvent être plus coûteuses à l'achat que les alternatives en PEHD ou en métal. Leur utilisation est donc généralement justifiée dans des situations où leurs propriétés uniques apportent un avantage significatif, comme dans les installations offshore ou les environnements chimiques agressifs.
Additifs anti-UV : prolongation de la durée de vie des cuves plastiques
L'utilisation d'additifs anti-UV dans la fabrication des cuves plastiques est une innovation importante qui prolonge considérablement leur durée de vie, en particulier pour les installations extérieures. Ces additifs protègent le plastique contre la dégradation causée par l'exposition prolongée aux rayons ultraviolets du soleil, qui peuvent fragiliser le matériau au fil du temps.
Les additifs anti-UV fonctionnent en absorbant les rayons UV nocifs avant qu'ils ne pénètrent dans le plastique, ou en dispersant l'énergie UV de manière à minimiser ses effets néfastes. Cette protection est essentielle pour maintenir l'intégrité structurelle de la cuve et prévenir les fuites ou les fissures qui pourraient résulter d'une dégradation due aux UV.
Il est important de noter que même avec des additifs anti-UV, une inspection régulière des cuves plastiques reste nécessaire pour détecter tout signe de dégradation. De plus, le choix d'un emplacement approprié, à l'abri de l'exposition directe au soleil lorsque possible, peut contribuer à prolonger davantage la durée de vie de la cuve.
Cuves à double paroi : sécurité renforcée et détection des fuites
Les cuves à double paroi représentent une avancée significative dans la sécurité du stockage de carburant. Elles consistent en deux cuves, l'une à l'intérieur de l'autre, avec un espace interstitiel entre les deux. Cette conception offre une protection supplémentaire contre les fuites et facilite la détection précoce de tout problème d'étanchéité.
Le principal avantage des cuves à double paroi est leur capacité à contenir toute fuite potentielle de la cuve intérieure, évitant ainsi la contamination du sol et des eaux souterraines. Cette caractéristique est particulièrement importante dans les zones écologiquement sensibles ou là où les réglementations environnementales sont strictes.
De plus, l'espace interstitiel entre les deux parois permet également l'installation de systèmes de détection de fuites sophistiqués, offrant une surveillance continue de l'intégrité de la cuve. Cette technologie permet une intervention rapide en cas de problème, minimisant ainsi les risques environnementaux et les coûts associés aux déversements.
Systèmes de surveillance par vide : technologie bundreno pour la détection précoce
La technologie Bundreno représente une avancée significative dans les systèmes de surveillance des cuves à double paroi. Ce système utilise le vide pour détecter rapidement toute fuite, offrant une solution fiable et précise pour la sécurité du stockage de carburant. Le principe est simple mais efficace : un vide est maintenu dans l'espace interstitiel entre les deux parois de la cuve. Toute perte de vide indique une brèche potentielle dans l'une des parois.
L'un des principaux avantages du système Bundreno est sa capacité à détecter des fuites extrêmement petites, bien avant qu'elles ne deviennent un problème majeur. Cette détection précoce permet une intervention rapide, réduisant considérablement les risques de contamination environnementale et les coûts associés aux réparations majeures. De plus, le système fonctionne en continu, offrant une surveillance 24/7 sans intervention humaine régulière.
Il est important de noter que l'installation d'un système Bundreno nécessite une expertise technique spécifique pour garantir son bon fonctionnement. De plus, des contrôles périodiques sont recommandés pour vérifier l'intégrité du système lui-même. Malgré ces considérations, l'investissement dans une telle technologie est souvent justifié par la tranquillité d'esprit et la conformité réglementaire qu'elle apporte.
Interstitiel en brique réfractaire : alternative traditionnelle pour double paroi
L'utilisation de briques réfractaires dans l'espace interstitiel des cuves à double paroi représente une alternative plus traditionnelle aux systèmes de surveillance par vide. Cette méthode, bien qu'ancienne, reste efficace pour certaines applications spécifiques. Les briques réfractaires offrent une excellente résistance thermique et chimique, ce qui les rend particulièrement adaptées pour le stockage de carburants à haute température ou de produits chimiques agressifs.
L'un des principaux avantages de l'interstitiel en brique réfractaire est sa durabilité. Ces briques peuvent résister à des conditions extrêmes pendant de longues périodes sans se dégrader. De plus, en cas de fuite de la paroi intérieure, les briques réfractaires peuvent absorber une partie du produit, ralentissant ainsi sa propagation et facilitant la détection visuelle lors des inspections.
Cependant, il est important de noter que cette méthode ne permet pas une détection automatique des fuites comme le font les systèmes de surveillance par vide. Des inspections régulières sont donc essentielles pour garantir l'intégrité de la cuve. De plus, la réparation ou le remplacement des briques réfractaires peut s'avérer complexe et coûteux en cas de contamination importante.
Réglementation ICPE : exigences pour les installations classées
La réglementation ICPE (Installations Classées pour la Protection de l'Environnement) joue un rôle crucial dans l'encadrement du stockage de carburant en France. Cette réglementation vise à prévenir les risques environnementaux et sanitaires liés aux activités industrielles, dont le stockage de substances dangereuses comme les carburants. Pour les cuves de stockage de carburant, les exigences ICPE varient en fonction de la nature et de la quantité de produits stockés.
Les principales exigences de la réglementation ICPE pour les cuves de carburant incluent :
- L'obligation d'une double paroi ou d'un bac de rétention pour les cuves de grande capacité
- La mise en place de systèmes de détection de fuites
- Des inspections périodiques obligatoires
- Des normes strictes concernant l'implantation et la distance par rapport aux zones sensibles
Il est crucial pour les exploitants de se conformer à ces réglementations, non seulement pour éviter les sanctions, mais aussi pour garantir la sécurité de leurs installations et la protection de l'environnement. La non-conformité peut entraîner des pénalités sévères et, dans certains cas, la fermeture de l'installation.
Dimensionnement et installation des cuves de carburant
Le dimensionnement et l'installation appropriés des cuves de carburant sont des étapes critiques pour assurer un stockage sûr et efficace. Un dimensionnement inadéquat peut entraîner des problèmes de surcapacité coûteuse ou, à l'inverse, des ruptures de stock fréquentes. De même, une installation incorrecte peut compromettre la sécurité et la conformité réglementaire de l'ensemble du système de stockage.
Calcul de la capacité : facteurs de consommation et stockage stratégique
Le calcul précis de la capacité de stockage nécessaire est une étape fondamentale dans le choix d'une cuve à carburant. Ce calcul doit prendre en compte plusieurs facteurs clés :
- La consommation moyenne quotidienne ou hebdomadaire
- Les fluctuations saisonnières de la demande
- Les délais de réapprovisionnement
- Les exigences réglementaires spécifiques à votre secteur
Un stockage stratégique implique de trouver l'équilibre entre avoir suffisamment de carburant pour éviter les ruptures et ne pas immobiliser trop de capital dans des stocks excessifs. Il est recommandé de prévoir une capacité de stockage correspondant à 1,5 à 2 fois votre consommation moyenne entre deux livraisons. Cette marge permet de faire face aux imprévus et aux variations de consommation.
Implantation géographique : contraintes environnementales et réglementaires
L'implantation géographique d'une cuve de carburant doit respecter des contraintes environnementales et réglementaires strictes. Les principaux facteurs à considérer sont :
1. La distance par rapport aux zones sensibles (cours d'eau, nappes phréatiques, habitations)
2. L'accessibilité pour les véhicules de livraison et d'intervention d'urgence
3. La protection contre les risques naturels (inondations, glissements de terrain)
4. La conformité avec les plans locaux d'urbanisme
Il est essentiel de consulter les autorités locales et les experts en environnement lors de la phase de planification. Une étude d'impact environnemental peut être nécessaire pour les installations de grande envergure. L'objectif est de minimiser les risques pour l'environnement tout en optimisant l'efficacité opérationnelle de l'installation.
Systèmes de rétention : bacs et digues conformes à l'arrêté du 22 juin 1998
Les systèmes de rétention sont une composante cruciale de la sécurité des installations de stockage de carburant. L'arrêté du 22 juin 1998 définit les exigences spécifiques pour ces systèmes en France. Les principales dispositions incluent :
- La capacité de rétention doit être au moins égale à la plus grande des deux valeurs suivantes : 100% de la capacité du plus grand réservoir ou 50% de la capacité totale des réservoirs associés.
- Les parois de la rétention doivent être étanches et résister à la pression statique du liquide susceptible d'être retenu.
- Le système doit être équipé de moyens de détection de fuite et d'alarme.
Le choix entre un bac de rétention intégré à la cuve ou une digue de rétention externe dépend de plusieurs facteurs, notamment l'espace disponible, le type de cuve et les contraintes opérationnelles. Dans tous les cas, il est impératif de s'assurer que le système de rétention est régulièrement inspecté et entretenu pour garantir son efficacité en cas d'incident.
Maintenance et sécurité des cuves de stockage de carburant
La maintenance régulière et les mesures de sécurité appropriées sont essentielles pour garantir l'intégrité et la longévité des cuves de stockage de carburant. Une maintenance négligée peut entraîner des fuites, des contaminations, voire des accidents graves. De même, des mesures de sécurité inadéquates peuvent mettre en danger non seulement l'installation, mais aussi le personnel et l'environnement.
Inspections périodiques : fréquence et procédures selon la norme NF EN 13160
La norme NF EN 13160 établit les lignes directrices pour les systèmes de détection de fuites et les procédures d'inspection des cuves de stockage. Selon cette norme, les inspections périodiques doivent être effectuées à des intervalles réguliers, généralement :
- Inspection visuelle mensuelle pour détecter toute anomalie apparente
- Test d'étanchéité annuel pour vérifier l'intégrité de la cuve
- Inspection approfondie tous les 5 ans, incluant des tests non destructifs
Ces inspections doivent être réalisées par des professionnels qualifiés et documentées de manière exhaustive. Tout écart par rapport aux normes doit être immédiatement corrigé pour maintenir la conformité et la sécurité de l'installation.
Nettoyage et dégazage : protocoles pour l'élimination des résidus
Le nettoyage et le dégazage des cuves de carburant sont des opérations délicates qui nécessitent des protocoles stricts pour garantir la sécurité et l'efficacité. Ces procédures sont essentielles avant toute opération de maintenance, de réparation ou de mise hors service d'une cuve. Les étapes principales incluent :
1. La vidange complète de la cuve
2. Le dégazage pour éliminer les vapeurs inflammables
3. Le nettoyage mécanique ou chimique pour éliminer les résidus
4. La gestion sécurisée des déchets et effluents
Il est impératif que ces opérations soient réalisées par des professionnels certifiés, équipés du matériel approprié et respectant scrupuleusement les normes de sécurité. L'utilisation d'équipements antidéflagrants et de protections individuelles adaptées est obligatoire pour prévenir tout risque d'incendie ou d'intoxication.
Équipements de sécurité : vannes, jauges et systèmes anti-débordement
Les équipements de sécurité jouent un rôle crucial dans la prévention des accidents et la gestion des risques liés au stockage de carburant. Parmi les éléments essentiels, on trouve :
- Les vannes de sécurité : Elles permettent d'isoler rapidement la cuve en cas d'urgence. Les vannes à fermeture automatique sont particulièrement recommandées pour une réaction rapide en cas d'incident.
- Les jauges de niveau : Elles fournissent une indication précise du niveau de carburant dans la cuve. Les systèmes de télémétrie modernes permettent un suivi en temps réel et peuvent déclencher des alertes en cas de niveau bas ou de variations suspectes.
- Les systèmes anti-débordement : Ces dispositifs sont conçus pour arrêter automatiquement le remplissage de la cuve lorsqu'elle atteint sa capacité maximale. Ils sont essentiels pour prévenir les déversements lors des opérations de livraison.
L'installation et la maintenance régulière de ces équipements sont cruciales pour garantir leur efficacité. Il est recommandé de procéder à des tests périodiques de tous les systèmes de sécurité et de former adéquatement le personnel à leur utilisation. La combinaison d'équipements fiables et d'une formation appropriée constitue la meilleure défense contre les incidents potentiels.